Pressure Regulation
Pressure regulation in pneumatics is vital for the correct operation of circuits and for damage prevention to circuit components. As you would imagine all pneumatic components have a maximum operating pressure.
Relief valves
These are basic pressure regulators and are usually used in pneumatic circuits as a backup device should the main pressure controller fail. They work with the use of a ball valve which is under an adjustable amount of pressure to keep the valve shut, once this pressure is exceeded the ball forces the spring back allowing the excess pressure to escape. Care should be taken when employing a pressure relief valve, this is because the valve must have sufficient ability to vent the pressure and flow quickly enough should a fault occur, and should the worst happen the relief valve may have to dump the entire compressor output.
Once a fault has triggered the release mechanism and the pressure has dropped sufficiently then the valve automatically closes and re-seals itself. This type of valve is always ready to release pressure again if needed, however a safety valve must be manually reset once it has cracked to release pressure.
Non-relieving pressure regulators
Non-relieving pressure regulators work by restricting flow rather then venting it should over pressure occur. The regulator restricts flow when the pressure gets too high because the pressure acts on the diaphragm forcing it up against the spring pressure, the diaphragm has what is called a ‘poppet’ attached on the end of it which is drawn up with the diaphragm and restricts the passing air flow.
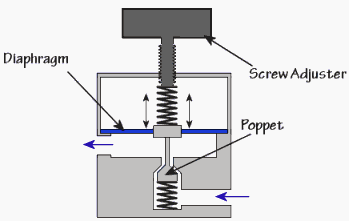
Relieving pressure regulators
Relieving pressure regulators use a similar diaphragm system to that of the non-relieving regulator. The diaphragm drops if the outlet pressure is too high closing the inlet valve and opening the outlet vent, releasing pressure until it falls back to the preset pressure.
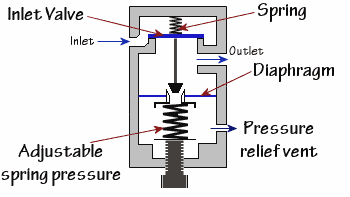
|