MIG Welding (Metal Inert Gas)
MIG welding is one of the more simple welding methods of metal welding as it does not require a high level of skill to achieve results. The process is semi-automatic because an electrode wire and gas are automatically fed through the gun at a user defined speed or pressure when the operator pulls down the trigger, the electronic arc can also be user defined and carried out automatically on operation. MIG is a quick and easy form of welding; it is used often by robotics in automated production lines. MIG however does not offer the best penetration when welding therefore is not the best choice for use on thick plates where a strong weld is required.
M.I.G. (Metallic Inert Gas)
This term is only strictly correct when the process being used with an inert gas for shielding purposes. E.g. Aluminium welding with a pure argon gas shield
M.A.G.S. (Metallic Arc Gas Shielding)
This process uses active gas shielding, for example when welding low carbon steel in conjunction with argon & Co2 gas shield.
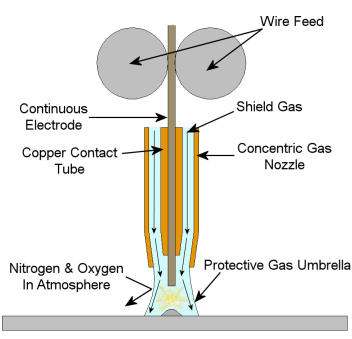
M.I.G. and M.A.G.S. Working Principle
A continuous consumable wire is fed through a suitable torch or gun which is used both as an electrode and a filler, the gun or torch embodies a concentric gas nozzle which channels a protective gas which is usually fed from a separate cylinder out and around the newly formed weld preventing atmospheric contamination. The weld is formed due to the positive electrode (the continuous wire) coming into close contact with the negative electrode of the work piece allowing a large current to flow through the wire causing the tip to heat up beyond its melting point.
M.I.G./M.A.G.S. Welding - Application Of Gases
The type of gas or gas mixtures employed in M.A.G.S. welding varies with the metal being joined. To some extent the gas is chosen to reduce costs, the inert gases being very expensive, but more often the gas is chosen for its effect on the arc characteristics, e.g. burn off rate, type of metal transfer and penetration. These important parameters play a large part in the selection of a shielding gas.
Here are some examples of shielding gases and their applications.
PURE ARGON 99.99% (Inert)
Supplied in peacock blue cylinders.
Applications: |
-Aluminium and its alloys
-Magnesium and its alloys
-Titanium and its alloys
-Nickel and its alloys
-Copper and its alloys
-9% Nickel steels |
Metal Transfer: |
Spray and pulsed |
|
ARGON with 1-2% OXYGEN (Active)
Supplied in peacock blue cylinders with a black horizontal band around the middle, the oxygen content would also be indicated on the cylinder label.
Applications:
|
Stainless Steel |
Metal transfer:
|
Dip, Spray and pulsed |
|
CARBON DIOXIDE (Co2) (Active)
This gas is supplied in liquid form in black cylinders, with a white vertical stripe indicating the siphon tube inside the cylinder. The oxygen content is high and this results in fierce arc characteristics as the oxygen is burnt up and the arc voltage increases. This gas is rarely used today as it has been superseded by gas mixtures such as argon Co2 which combine the advantages of both gases.
Applications:
|
Low carbon steels
Low alloy steels |
Metal transfer: |
Dip and spray |
|
Mig Welding Advantages
1) Higher welding speeds
2) Greater deposition rates
3) Less post welding cleaning (e.g. no slag to chip off weld)
4) Better weld pool visibility
5) No stub end losses or wasted man hours caused by changing electrodes
6) Low skill factor required to operate M.I.G / M.A.G.S welding torch
7) Positional welding offers no problems when compared to other processes. (Use dip or pulsed mode of transfer)
8) The process is easily automated
9) No fluxes required in most cases
10) Ultra low hydrogen process
Mig Welding Disadvantages
1) Higher initial setup cost
2) Atmosphere surrounding the welding process has to be stable (hence the shielding gasses), therefore this process is limited to draught free conditions
3) Higher maintenance costs due to extra electronic components
4) The setting of plant variables requires a high skill level
5) Less efficient where high duty cycle requirements are necessary
6) Radiation effects are more severe
|